INTRODUCTION
The conventional fuel additive industry has evolved over many generations however, the focus remains limited to engine performance. Typical features of most conventional fuel additives includes cetane boost, fuel lubricity enhancement, corrosion inhibitors and oxidation stabilizers.
While these features are attractive to any company operating diesel equipment and in fairness offers some level of improved fuel economy and performance. Unfortunately, consumers are confused by the hype and the hundreds of different brands that are out there. What does a consumer select as there are many different brands and a very generic message presented on every package?
More informed consumers are aware that diesel fuel, while it has its advantages, also has is achilles heel - water! Many have experienced fouled filters, degraded fuel that has been sitting in storage for sometime, a standby generator that will not start or engine shut down due to fouled fuel strainers, fuel lines and filters. In these cases, many have used biocides to help correct the problem without a full understanding of how to properly deploy the use of biocides.
A surge in "fuel polishing" has received a lot of hype; this is simply the filtering and removal of heavy contaminants from fuel. Unfortunately, this may be good money spent on a very temporary solution. Fuel Polishing does not remove the conditioning/biofilm that is lining the tank and once the fuel is re-introduced to the tank, the process of microbial biomass development starts all over again. In some cases, it can bloom immediately given the right conditions.
This final consideration that most are unaware of is the phenomena known to corrosion engineers as MIC or microbially influenced corrosion. This topic has been researched extensively and is a well known problem in aqueous and petroluem based storage systems. An interesting note is that filming amines have been used in the water treatment industry for decades to help prevent MIC - hmmm??? why not the Fuel Industry?
WHY FUEL RIGHT?
Fuel Right does not deploy conventional fuel additive ideology. In the mid 90's, a great deal of research was done on the use of amines as fuel additives. They had many functions including lubricity improver, stabilizer, enhanced fuel atomization, surfactant (detergency properties) and more. These studies typically looked at single amine chemistries to assess their use in fuel.
Bob Tatnall set out to accomplish one thing - to eliminate the microbial issues related to sludge in diesel fuel and home heating systems. His 30 years at DuPont studying materials, corrosion and MIC was the foundation on which he began to research a solution to the problem. 19 years later, Fuel Right has evolved to become a technical leader in solving a problem that is now becoming more apparent with the shift to ULSD.
Bob experimented with hundred of amines and figured out how to "dissolve" the problem. That's not all, the combined research of amines as a fuel additive has resulted in an additive technology that holistically manages the fuel storage and supply, delivery through strainers, fuel lines and filters and enhances engine performances far superior to any conventional additive or biocide.
FUEL RIGHT: FEATURES, ADVANTAGES & BENEFITS
- Dissolves, Disperses & Prevents Sludge Contamination That Clogs Fuel Lines, Filters & Strainers
- More Effective than Biocides or Conventional Fuel Additives - We have Test Data to Prove it!
- Cleans Tanks, Fuel Lines, Filters and Strainers
- Improves Fuel Economy
- Reduces Exhaust Particulate
- Restores Fuel Lubricity and Stabilizes Fuel in Storage
- Provides a Filming Amine Microscopic Corrosion Coating to Protect Fuel System Components
- Warranty Safe for all Diesel Engines
- EPA Registered
- Suitable for use in Diesel, Bio-Diesel and Marine Gas Oil
Along with Brookhaven National Laboratory, these tests were developed by Bob Tatnall to determine the effectiveness of fuel additives and intended to rank their relative ability to control sludge growth, keep metal surfaces clean and to protect steel tanks against corrosion.
See the results for yourself.
Fuel Right is now being used by major ferry corporations, workboat companies, mining companies, heavy trucking, standby generators in the communications sector (cell towers), recreational marine, fuel wholesale and as a premium additive in diesel fuel at gas stations internationally. We are currently operating in 10 countries and our presence is growing rapidly.
We are now embarking on our next chapter of engine performance research which includes a very detailed examination of ignition, combustion, emission, power and torque in the next generation of diesel engines on the market. Stay tuned as we expect this to be a serious game changer.
Bacteria are natural residents in diesel fuel. They are most commonly introduced through vent tubes, water intrusion, and fuel transfer. Chemicals from water in the fuel form a conditioning film on solid surfaces. This occurs within minutes after the fuel has been introduced to the tank.
This film allows free-floating bacterial cells to attach to the surface (Stage 1), at which point some of them begin to generate a starch like substance often referred to as "slime"(Stage 2). This is the "glue" that holds the sludge or biomass together. Soon, other bacteria start to move into the slime layer (Stage 3).
Some of these get their food from the fuel, while others get their food from the by-products of the fuel users. The result is a rather complex ecology of life forms growing in the sludge (Stage 4). Some of these bacteria produce organic acids, which may promote pitting corrosion of underlying steel. The pitting corrosion, only observed under sludge accumulations, accounts for most fuel tank failures.
As sludge builds up, bits of it slough off and travel downstream (Stage 5), where they adhere to surfaces (Stage 6) - perhaps a filter - and start to grow new sludge. The most common indicator of a severely fouled fuel system is complete filter plugging resulting in engine shut-down.
Sessile Bacteria Attaching to Surfaces Within Fuel System
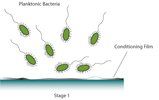
Bacteria Excrete
Slime-Forming Bacteria
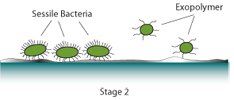
Complex Bacterial
Colonies Begin to Develop
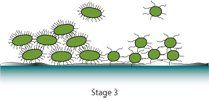
Complex Biofilm Development
Biocides are Rarely Effective
Against Established "Sludge"
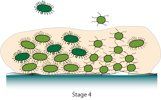
Biofilm Sloughing
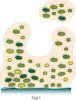
Sloughing - Redeposit on Filters, Fuel Lines & Strainers
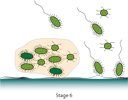
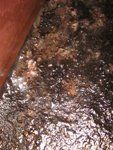
Bottom of a Marine Fuel Tank
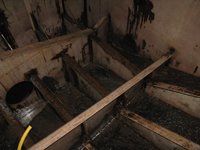
Draining Shows Excessive Bacterial Sludge
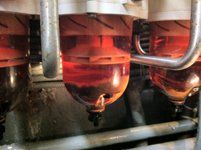
Sludge Contamination
Sludge in contact with steel or cast iron leads to corrosion. The exact role of the bacteria themselves is a matter of much research and conjecture, but it is clear that very high rates of metal penetration occur under biologically active sludge.\
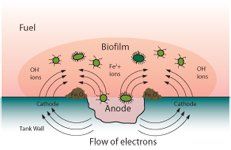
The presence of biofilm in fuel systems impact the environment that the fuel is residing in. Corrosion by-products may act as catalysts in the reaction that result in the oxidation of the fuel. Free-floating acids are also a contributor to fuel oxidation.
Did you know that the presence of biofilm can affect the following?
- Decrease in corrosion inhibitor additive effectiveness
- Decrease anti-oxidant additive effectiveness
- Reduce lubricity additive effectiveness
- Decrease fuel's oxidative stability
- Boost a fuel's peroxide number
- Boost a fuel's total acid number (TAN)
- Increase fuel's corrosivity
Bits of sludge that have landed on a filter will grow and slowly blanket the filter, sealing it off and stopping the flow of fuel. These growths may initially appear as tiny specs and not readily visible to the naked eye. As biofilm is transparent, the color of the contamination is a good indicator of what issues are going on in the tank. A black contaminated filter is evidence of degraded fuel while a rust coloured filter is evidence of severe corrosion. The three example below are samples of each case.
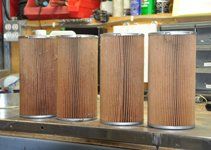
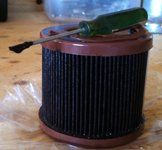
sludge problem.
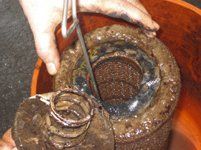
Diesel engine technology is evolving and fuel is changing. ULSD has been stripped of lubricity and oxidative stability has been compromised. Newer tier engines operate with a common rail fuel delivery system with piezoelectric injectors. Pressure are extremely high and the injectors operate with extremely tight tolerances.
Using dirty fuel in new and old engines leads to premature component failure, injectors operating inefficiently and reduced fuel economy. Conventional fuel additives today typically promote lubricity and performance using 2-EHN (2 Ethylhexyl Nitrate) cetane boost. While this helps performance at the engine, this ignores the issues in the tank and through the delivery system (strainers, fuel lines and filters)
Fuel Right takes a holistic approach at managing fuel completely through the system from the tank through delivery and performance. Fuel Right offers total fuel coverage!
Our unique Fuel Right® chemistry has NEVER failed our customers. Over the past 15 years, and more than 5 billion litres treated, many significant, vexing problems have been resolved. A summary from diverse applications is provided below – we welcome the opportunity to share additional “success” stories with you!
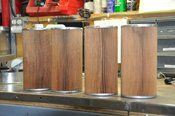
Mike Hinds, owner of Hinds Oil Company, Montrose Pennsylvania
Vincent Borello, Moran Towing Company
Leo Bickham, Owner, Leo’s Boats
Ed Hermann, Port Engineer, Weeks Marine
Charles Crawford, Port Engineer, Reinhauer Transportation
Smitty, Atlantic Bulk Carriers, Middletown, DE
Jim Dingus, Pallet One, Livermore Falls, ME
Bill Engle, Service Mgr., Berwyn, Coatesville, Parksburg, PA
Ken Reardon, Owner, Ken’s Oil Service, Danvers. MA
Gary Steer, Service Manager, Fredericks Fuel - Oakridge, NJ